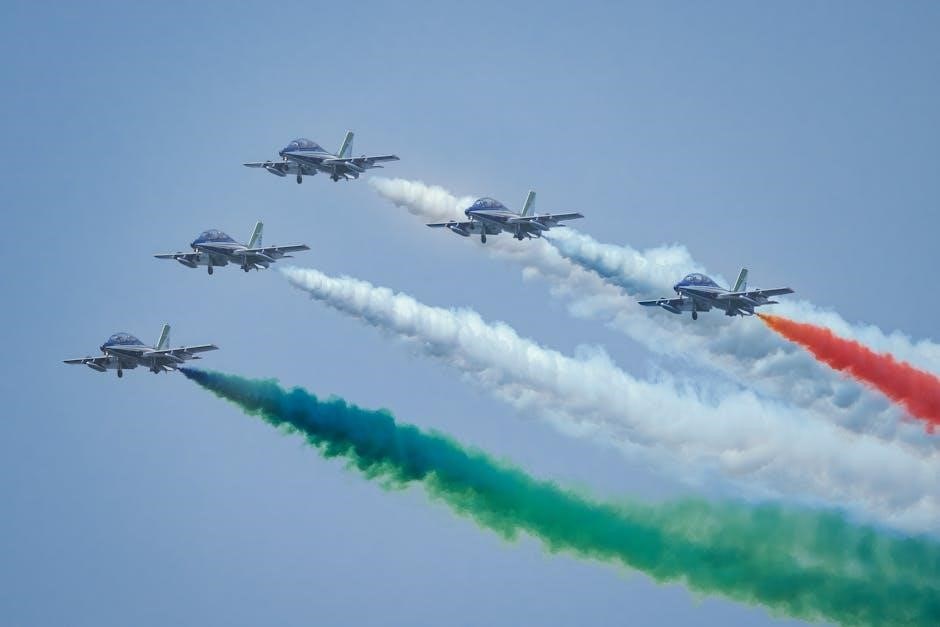
aircraft bulkhead pdf
Aircraft bulkheads are critical structural components that separate sections of the fuselage, providing support and maintaining air pressure in pressurized cabins. They ensure safety and structural integrity.
1.1 Definition and Purpose of Bulkheads in Aircraft
Aircraft bulkheads are structural partitions within the fuselage, dividing it into sections to maintain air pressure, redistribute loads, and provide support. They act as barriers between pressurized and unpressurized zones, ensuring cabin pressure is sustained. Bulkheads also serve as attachment points for wings, engines, and other components, enhancing structural integrity. Their primary purpose is to optimize safety, efficiency, and performance by isolating sections and managing stress distribution across the aircraft.
1.2 Importance of Bulkheads in Maintaining Structural Integrity
Bulkheads are essential for maintaining the structural integrity of an aircraft by redistributing concentrated loads, such as wing and engine forces, across the fuselage. They prevent deformation under pressure and stress, ensuring the aircraft’s shape and stability. Additionally, bulkheads act as barriers to contain pressure in cabins, protecting passengers and systems. Their failure can lead to catastrophic structural compromise, making them a critical component in aircraft design and safety.
Types of Aircraft Bulkheads
Aircraft bulkheads are categorized into pressure and non-pressure types. Pressure bulkheads, such as front and rear bulkheads in pressurized cabins, withstand pressure loads. Non-pressure bulkheads provide structural support in unpressurized sections.
2.1 Pressure Bulkheads: Front and Rear Bulkheads in Pressurized Cabins
Pressure bulkheads are essential in aircraft with pressurized cabins, located at the front and rear. These structural components maintain cabin pressure, prevent collapse, and support equipment installation. They are designed to endure significant stress, ensuring passenger safety and comfort. Dome-shaped bulkheads are often preferred due to their ability to distribute pressure loads efficiently, making them critical for aircraft performance and safety in pressurized environments.
2.2 Non-Pressure Bulkheads: Structural Support in Unpressurized Sections
Non-pressure bulkheads provide structural support in unpressurized sections of the aircraft, such as cargo areas or rear compartments. These components help in load distribution, prevent fuselage deformation, and serve as attachment points for wings and landing gear. Unlike pressure bulkheads, they don’t bear the load of pressurization but are crucial for maintaining overall aircraft integrity and ensuring operational efficiency in non-pressurized zones. Their design is optimized for strength and durability without the need for pressure containment.
Design Approaches for Aircraft Bulkheads
Aircraft bulkhead design approaches are crucial for ensuring structural integrity, weight reduction, and aerodynamic efficiency. They involve flat or dome-shaped structures, advanced materials, and finite element analysis (FEA) for optimal performance and safety.
3.1 Flat vs. Dome-Shaped Bulkheads: Advantages and Disadvantages
Flat bulkheads are simpler to manufacture and cost-effective, offering straightforward integration with surrounding structures. However, they may lack the strength needed for high-pressure environments. Dome-shaped bulkheads, with their curved surfaces, excel in distributing pressure loads and are preferred in pressurized cabins. Despite their structural advantages, dome-shaped designs are complex to fabricate and may require more space, making them less suitable for certain aircraft configurations.
3.2 Material Selection for Bulkhead Construction
Material selection for aircraft bulkheads is critical to ensure strength, durability, and weight efficiency. Aluminum alloys, such as 2024 T351, are commonly used due to their high strength-to-weight ratio and corrosion resistance. For modern aircraft, advanced composites like carbon fiber-reinforced polymers (CFRP) are increasingly favored for their superior strength and lighter weight. The choice of material depends on the bulkhead’s location, load requirements, and operational conditions, ensuring optimal performance and safety while minimizing maintenance needs.
3.3 Finite Element Analysis (FEA) in Bulkhead Design
Finite Element Analysis (FEA) is a crucial tool in bulkhead design, enabling engineers to simulate stress, strain, and deformation under various loads. FEA helps optimize structural performance by identifying weak points and ensuring compliance with safety standards. By analyzing pressure, bending, and fatigue loads, designers can refine bulkhead shapes and materials efficiently. This method reduces prototyping costs and accelerates certification, ensuring reliable and lightweight structures that meet operational demands while maintaining passenger safety and aircraft performance.
Structural Analysis of Aircraft Bulkheads
Structural analysis ensures bulkheads withstand stress, pressure, and fatigue, maintaining aircraft integrity and safety under various operational conditions and loads.
4.1 Stress Analysis and Load Distribution
Stress analysis of aircraft bulkheads involves evaluating how loads are distributed across the structure, ensuring it can withstand pressure, bending, and shear forces. Finite element analysis (FEA) is commonly used to simulate stress distribution, identifying critical points where material failure might occur. The shape of the bulkhead, whether flat or dome-shaped, significantly impacts load distribution. Dome-shaped bulkheads are preferred for their ability to evenly distribute pressure loads, reducing stress concentrations. Accurate stress analysis is crucial for maintaining structural integrity and ensuring passenger safety during flight operations.
4.2 Fatigue Analysis and Durability Testing
Fatigue analysis is essential for assessing the long-term durability of aircraft bulkheads, as repetitive stress from flight cycles can lead to material degradation. Advanced simulation tools and experimental testing are employed to evaluate the bulkhead’s resistance to fatigue cracking. Durability testing involves subjecting the structure to simulated flight loads, ensuring it meets safety standards over its operational life. The findings inform maintenance schedules and design improvements, ensuring the bulkhead remains reliable and safe throughout the aircraft’s service life.
4.3 Impact of Bulkhead Design on Aircraft Performance
Bulkhead design significantly influences aircraft performance, affecting weight distribution, aerodynamics, and fuel efficiency. Optimized bulkheads reduce drag and enhance structural efficiency, contributing to improved fuel economy. Lightweight materials and streamlined shapes minimize weight while maintaining strength, crucial for overall aircraft efficiency. Additionally, bulkhead placement impacts cabin pressurization and passenger comfort, making their design integral to balancing performance with operational requirements. Efficient bulkhead design is thus vital for achieving optimal aircraft performance and meeting modern aviation standards.
Manufacturing and Maintenance of Bulkheads
Bulkheads are manufactured using advanced techniques like CNC machining and composite layup. Regular inspections, repairs, and compliance with FAA guidelines ensure structural integrity and safety over time.
5.1 Modern Manufacturing Techniques for Bulkheads
Modern bulkhead manufacturing employs advanced CNC machining, 3D printing, and composite material layup. These techniques ensure precision, reduce weight, and enhance durability. Finite element analysis optimizes designs, while automated systems improve efficiency. Use of high-strength materials like aluminum alloys and carbon fiber composites is common. CAD software aids in creating complex shapes, such as dome-shaped bulkheads, which better withstand pressure loads. These methods ensure bulkheads meet stringent aerospace standards and performance requirements.
5.2 Inspection and Maintenance Requirements
Regular inspections of aircraft bulkheads are essential to ensure structural integrity and safety. Non-destructive testing (NDT) methods, such as ultrasonic and radiographic inspections, are used to detect cracks or damage. Visual inspections by certified personnel are also conducted to identify surface defects. High-stress areas, like attachment points, require frequent checks to prevent fatigue. Adhering to FAA guidelines ensures compliance with safety standards. Maintenance routines include cleaning and surface protection to prevent corrosion, ensuring the bulkhead’s longevity and performance.
5.3 Case Studies of Bulkhead Replacement and Repair
Case studies highlight the complexity of bulkhead replacement and repair. For instance, the Boeing 767-200 freighter underwent a rear pressure bulkhead replacement, ensuring structural integrity. Advanced materials like CFRP were used to enhance durability. Another case involved the Boeing 787, where aft bulkhead cracks prompted a redesign. These examples demonstrate the importance of adhering to FAA guidelines and utilizing modern manufacturing techniques to ensure safety and performance. Such studies provide valuable insights for future bulkhead design and maintenance.
Safety Regulations and Standards for Bulkheads
Safety regulations for aircraft bulkheads ensure structural integrity and airworthiness. The FAA enforces strict guidelines, including inspections and certifications, to maintain passenger and crew safety.
6.1 Federal Aviation Administration (FAA) Guidelines
The Federal Aviation Administration (FAA) establishes rigorous guidelines for aircraft bulkheads to ensure safety and durability. These regulations include mandatory inspections, material standards, and design criteria. The FAA requires that all bulkheads, particularly in pressurized cabins, must withstand extreme pressure loads and structural stresses. Compliance with these guidelines is critical for certification and operational approval. The FAA also mandates regular maintenance and inspection protocols to prevent failures and ensure continued airworthiness.
6.2 International Civil Aviation Organization (ICAO) Standards
The International Civil Aviation Organization (ICAO) sets global standards for aircraft bulkheads, focusing on safety, design, and performance. These standards ensure uniformity across countries and manufacturers. ICAO guidelines emphasize robust structural integrity, material quality, and fatigue resistance. They also outline testing procedures and certification processes. Compliance with ICAO standards is essential for international operations, facilitating harmonized safety practices worldwide. These standards are regularly updated to reflect advancements in technology and industry best practices.
6.3 Compliance and Certification Processes
Compliance and certification processes for aircraft bulkheads involve rigorous testing and inspections to ensure adherence to safety standards. Manufacturers must submit designs and materials for regulatory approval. Testing includes structural integrity, fatigue resistance, and pressure load capacity. Documentation and traceability are critical throughout the process. Certification is granted only after meeting all specified requirements, ensuring safe and reliable operation. Ongoing compliance involves periodic inspections and updates to maintain certification, reflecting evolving safety standards and technological advancements.
Applications of Bulkheads in Different Aircraft Types
Bulkheads are essential in commercial airliners for pressurization and structural support. Military aircraft use them for cargo separation and safety. General aviation relies on them for lightweight durability.
7.1 Bulkheads in Commercial Airliners
Bulkheads in commercial airliners are vital for maintaining pressurized cabins and structural integrity. They are typically located at the front and rear of the fuselage, withstanding pressure loads while separating passenger and cargo sections. These bulkheads ensure the aircraft’s shape is maintained and provide attachment points for wings and landing gear. Modern designs often use lightweight materials like aluminum alloys and composites to optimize performance. Finite Element Analysis (FEA) is commonly employed to ensure durability and safety under various flight conditions.
7.2 Bulkheads in Military and Special-Purpose Aircraft
Bulkheads in military and special-purpose aircraft are designed for extreme durability and versatility. These aircraft often require robust bulkheads to withstand combat conditions, payload stresses, and rapid deployment needs. Unlike commercial airliners, military bulkheads may incorporate customizable compartments for equipment storage and mission-specific hardware. Advanced materials like high-strength alloys and composites are used to ensure lightweight yet resilient structures. Rigorous testing and adherence to military standards ensure these bulkheads can endure harsh environments and sudden pressure changes, critical for operational success.
7.3 Bulkheads in General Aviation Aircraft
Bulkheads in general aviation aircraft are essential for structural integrity and functionality. They separate the cockpit from the cabin, support aircraft systems, and provide mounting points for equipment. Unlike larger commercial planes, these bulkheads are typically simpler in design, focusing on weight reduction and cost efficiency. Materials like aluminum alloys are commonly used, ensuring durability while maintaining affordability. Regular inspections are crucial to uphold safety standards, as these aircraft often operate in diverse conditions, requiring reliable performance and minimal maintenance.
Future Trends in Bulkhead Design and Technology
Future trends include advanced materials like composites, smart structures with sensors, and digital design tools for optimized efficiency. These innovations enhance performance and reduce weight in aviation.
8.1 Use of Advanced Materials and Composites
Advanced materials like carbon fiber reinforced polymers (CFRP) and lightweight alloys are being increasingly used in bulkhead construction. These composites offer superior strength-to-weight ratios, enhancing durability while reducing overall aircraft weight. Recent studies highlight the potential of CFRP for rear pressure bulkheads, improving resistance to fatigue and stress; Additionally, hybrid materials are being explored to optimize performance under various load conditions. The use of such advanced materials is expected to significantly improve bulkhead efficiency and contribute to safer, more fuel-efficient aircraft designs.
8.2 Integration of Smart Structures and Sensors
The integration of smart structures and sensors into aircraft bulkheads is revolutionizing maintenance and safety. Sensors embedded in bulkheads monitor stress, fatigue, and potential damages in real-time, enabling predictive maintenance. These smart systems detect anomalies early, reducing downtime and enhancing safety. Advanced sensors also optimize load distribution and structural health monitoring. By integrating these technologies, bulkheads become intelligent components, improving overall aircraft performance and reducing the need for manual inspections. This innovation is key to developing smarter, more efficient, and safer aircraft designs.
8.3 Impact of Digital Design Tools on Bulkhead Development
Digital design tools have significantly enhanced the development of aircraft bulkheads by enabling precise modeling and simulation. Software like CATIA V5 allows engineers to create detailed 3D models and simulate stress loads, improving accuracy. Finite Element Analysis (FEA) optimizes bulkhead design for strength and weight reduction. These tools also streamline the design-to-manufacturing process, reducing errors and production time. By leveraging digital technologies, manufacturers can create efficient, lightweight bulkheads that meet modern aviation demands while ensuring safety and performance standards are exceeded.